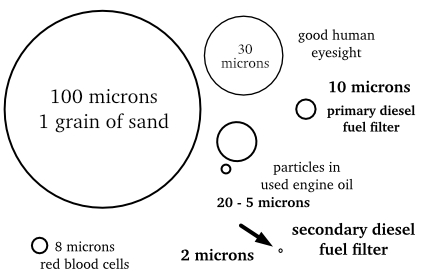
7 tips to ensure your engine will be running smooth all year long
Lack of clean fuel is the main cause of engine running problems—and the most easily avoided trouble! Diesel engines require very clean fuel because the fuel acts as a lubricant inside the injection pump and injectors. Tolerances between metal parts are very small (down to 0.2 microns in some pumps, compared to 100 microns for a grain of sand).
These six steps, or precautions, can help ensure that only scrupulously clean fuel reaches the injection pump and injectors:
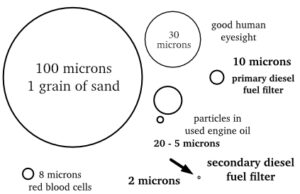
1) Buy clean fuel from a reliable source
Avoid refueling within three hours of a fuel delivery at a service station; waiting allows any debris and water stirred up in the station’s tanks to settle. Contamination should be suspected if buying from fuel drums, which may leak rainwater; fuel barges, which may have a leak; or in many smaller communities outside North America and Europe. If necessary, fill clean jerry cans with the fuel and allow to stand overnight. Any debris and water will settle to the bottom and clean diesel can be syphoned out.
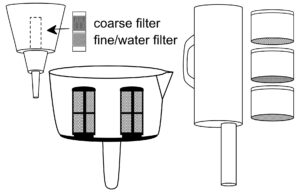
2) Use a filter funnel to pre-filter fuel before it goes into the tank(s)
Filter funnels are inexpensive and take out water and larger sediments. Using a filter-funnel will slow the process of filling the tank, so best done when the marina pump is not busy!
Check that the O-ring of the deck fuel fitting is not kinked when tightened.
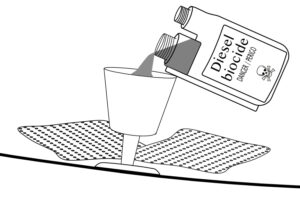
3) Add a preventive dose of biocide to mix with the diesel while fueling
Biocide kills hydrocarbon utilizing microorganisms (bacteria, fungi and yeasts—collectively known as “HUM”) which live in the fuel/water interface and feed on the carbon in diesel. HUM can grow very fast in warm conditions. HUM slime will plug filters and hoses, starving the injection pump of fuel and stopping the engine. The entire fuel circuit will need to be cleaned out after a HUM infestation; prevention is easier.
4) Change the primary fuel filter element regularly
The primary fuel filter, fitted between the tank and the engine’s lift (transfer) pump, is the main defense to prevent dirt and water reaching the engine.
This essential filter is not provided by engine manufacturers and must be installed by the boatbuilder or boatowner. Filter units come in different physical sizes and different sizes of fuel filtration. Some units have an easy-to-change top-loading replaceable element, others a spin-on disposable canister. The filter element should be 10 microns. Centrifugal force separates water from the fuel in the filter bowl which should be inspected regularly and drained, if necessary.
Do not wait for the filter element to look dirty; most of the particles the filter is removing are too small to see with the human eye. Changing once a season, or more often if contamination is suspected or the engine is running many hours, is an inexpensive precaution. Keep a few spare filters on board. A vacuum gauge fitted to the filter unit will give an accurate indication of when the filter needs to be changed. Be careful not to kink the O-rings on the filter assembly—air can be sucked into the system.
In general, the larger the primary fuel filter the better—if it fits in the space available. A small filter can be quickly overwhelmed by sludge stirred up in a seaway, potentially stopping the engine at a critical time. A larger filter that’s easy to access, with a filter element that’s easy to change, makes regular inspection and maintenance more likely and can be a worthwhile upgrade.
5) Check if the fuel pump (lift or transfer pump) has a wire gauze screen
This information should be in the engine manual. This screen is coarse (typically 70 microns) but can clog with gunge over time. Checking and cleaning should be part of an annual inspection.
6) Replace the secondary fuel filter (on-engine fuel filter) at least every second change of the primary filter
This is the last defense to prevent dirt or HUM slime reaching the injection pump. The filter either uses a replaceable element or a canister (similar to a small oil filter). The filter element should be two microns; however few manufacturers state the micron size on their replacement canisters.
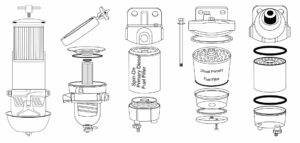
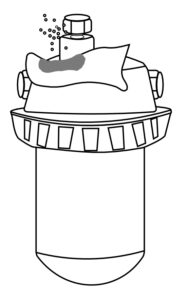
7) Bleed air from the system every time the fuel circuit is opened
A good time to do this is after you change a fuel filter. Open the bleed screw half a turn on the top of the secondary filter. Most lift pumps have a small manual pump to move fuel. As the handle is pumped, air and some fuel will bubble out of the bleed screw. Wrap a rag or paper towel around the filter to catch the fuel. Pump until only fuel, and no air, comes out. Then re-tighten the bleed screw. (If the pump handle will not move, the engine needs to be manually rotated half a turn to allow the pump diaphragm to move.)
Some engines bleed air automatically. Older engines will require manual bleeding. This is a useful skill to practice. Even a little air can stop any engine from starting or running. Make sure all hose clamps are tight. A small leak between the tank and the lift pump will allow air into the system. A leak after the lift pump will show as a fuel drip; it can also allow air into the system when the engine is stopped.
The injection pump and injectors will also need to be bled if, a) the engine ran out of fuel, or b) the engine was hunting for fuel before stopping. Both conditions mean there could be air in the injections.
TAKING A LITTLE extra care when adding fuel and changing filters, on a well designed and installed fuel system, goes a long way to ensuring reliable running.